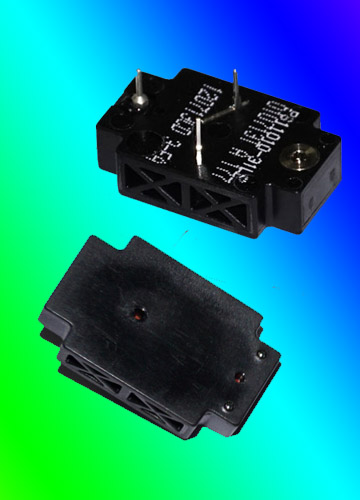
The central element is a Piezo-ceramic bending element which is built up of several layers, rather like a bimetallic strip. When an electrical voltage is applied, this element bends a few hundredths of a millimetre. This bending allows air to enter the piezo valve through port 1 to port 2. In the unactuated mode, the air can flow from port 2 to port 3. Depending on the voltage applied, the lesser or greater bending of the element generates an analogue pressure signal at port 2. The piezo valve can therefore be used either as a switching valve or as a proportional valve.
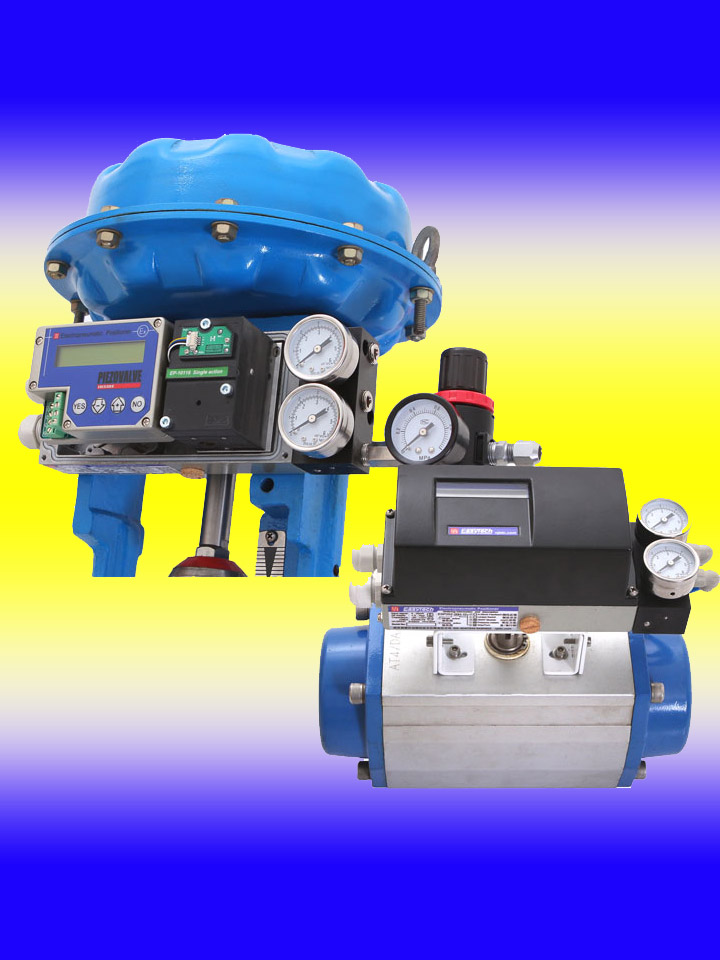
The intelligent electro-pneumatic positioner is two-wire designed,the power of positioner supplied from innput 4-20mA signal. The positioner assembled to linear or rotary actuator with mounting kit. The motion of the actuator is detected by a sensor which output the actual position value to microprocessor. According to the difference between setpoint and actual value, microprocessor outputs a PWM signal to the piezo valves,which regulate the flow of compress air into the actuator. When the signal lost, the postioner should be closed or fail in place.
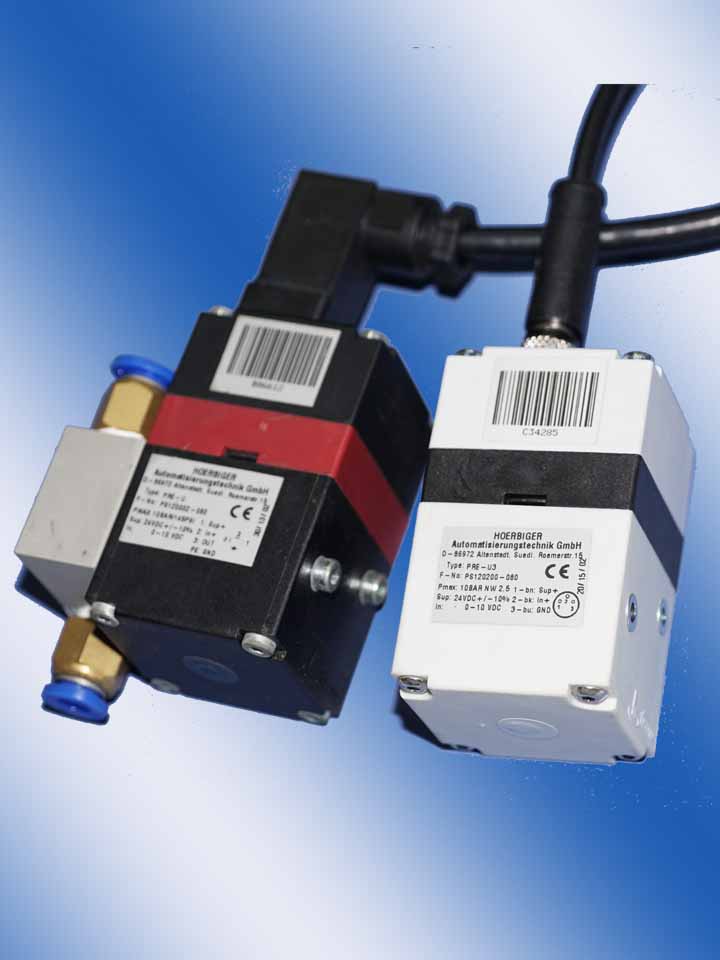
Electronically controlled pressure regulating
with actual value feedback.
The controler compares the setpoint with actual pressur and
consists of electronical closed loop control.
Compact dimension: 36x36x70mm/ 0.5% accuracy/ multi-range, Min. to 0.1bar.
Output : Pressure/Vcuum/Prsssur-Vacuum mixed
Voltage-controlled: 24V/0-10V @13mA
Current-controlled: 4-20mA, two wires
Serial-controlled : RS232
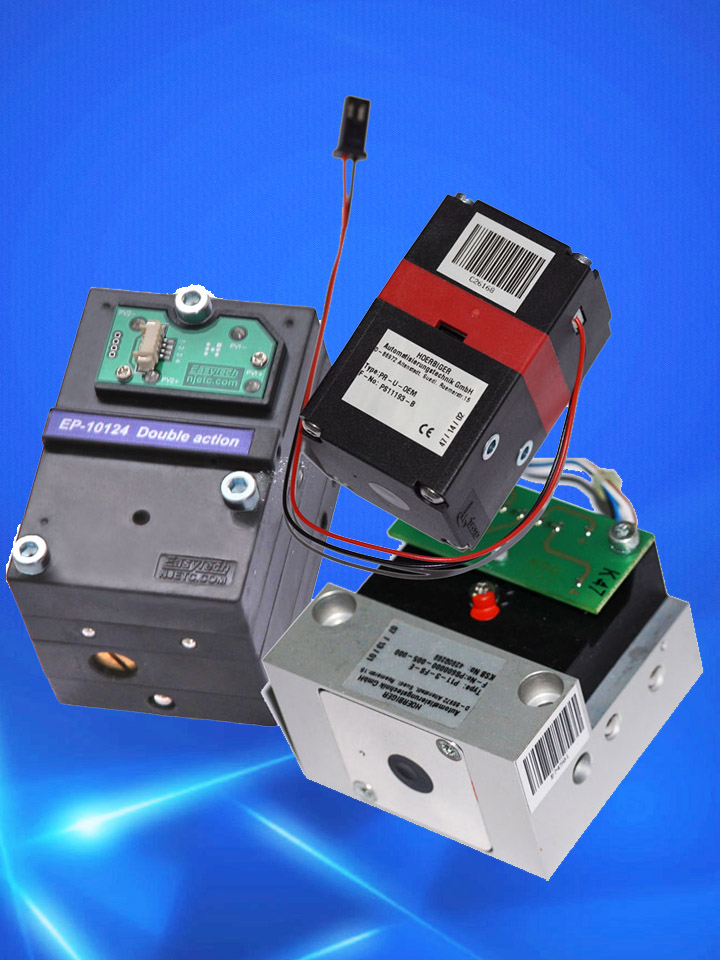
Two piezo valves are used as the pilot control elements.
They generate a pilot pressure in the pilot chamber of the pneumatic amplifier.
One piezo controls the import of pneumatic amplifier, another for exhaust,
therefore the flow derection can be efficently controlled by piezo valves.
E/P works at switch mode with faster response.
Power: 0-24VDC
Switching Current:10μA
Holding current: 0μA
Flow rate: 130L/Min
Response time: <2mS